Temperature Controllers, PID Control
More Information
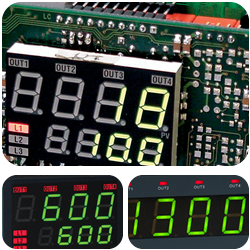
Our range of process controllers excel through outstanding control performance and very effective self-tuning capability.
- Choose from a wide range of software-selectable inputs, including
0-10V and 4-20mA - Obtain perfect control by chosing between 6 autotuning/ self-tuning functions via button on faceplate
- Switch between two setpoints (e.g. "Run" and "standby") via remote button or via button on instrument faceplate
- Know what the controller is doing : LEDs will flash when softstart or autotuning are in progress or when a sensor fault occurs
- Trigger pre-configured control functions (alarm reset, Auto Manual mode…) via remote switch
contact us to discuss your requirements.
Temperature & Universal Process Controllers
GEFRAN controllers are configurable microprocessor panel instruments that precisely control variables such as temperature, pressure, force, humidity, position, etc., with programmable alarms and optional communication interface.
Customisable operator interface, customisable scrolling messages and preventive diagnostics functions:
Configuration software
Enhanced software and hardware allow a high degree of user configurability.
The Gefran Express configuration software enables easy configuration from your PC. Features like loop break alarm and sensor fault detection, ramping, Auto / manual switching, plug-in output cards enable easy maintenance, and excellent abilities for combined Heat/Cool applications.
PID Temperature Control Loop: Heat-Cool Control
Application example: Plastic Blow Moulding Machine
The purpose of a temperature control loop is to maintain the process temperature accurately at a determined level.
![]() |
All parts in the control loop are essential and need to be selected, installed and set up correctly. It is particularly in combined heat-cool control applications where the advanced algorithms come into play, allowing an extremely narrow band between heating and cooling without causing overlap. By tuning the three parameters in the PID controller algorithm, the controller can provide control action designed for specific process requirements.
|
The response of the controller can be described in terms of the responsiveness of the controller to an error, the degree to which the controller overshoots the setpoint and the degree of system oscillation.
Some applications may require using only one or two actions to provide the appropriate process control. This is achieved by setting the other parameters to zero.
The 3 parameters that a PID controller uses for its algorithm based calculations, can be interpreted in terms of time:
- P (proportional): present error
- I (integral): accumulation of past errors
- D (derivative): prediction of future error based on the current rate of change.
Proportional
|
Integral
|
Derivative
|
The weighted sum of these three actions is used to adjust the process via a control element such as the power supplied to a heating element.
"PID controller" stands for "proportional, integral, derivative" control loop feedback mechanisms which are widely used in industrial control systems. The intelligence and configurability of PID controllers stems from its ability to calculate an "error value" as the difference between a measured process variable and the desired setpoint.
The controller can then send the appropriate commands to minimise the "error value" by adjusting the process control inputs. The algorithms used for this calculation involves three seperate constant parameters: The proportional , the integral and the derivative values: PID.
We offer a wide range of programmable process controllers to suit your requirements.
Need more insights and practical tips on how to optimally tune your PID controller the get the best production output?:
PID Training Request Contact us to discuss your requirements!